Sprayed Concrete
- Si Shen
- Nov 15, 2018
- 5 min read
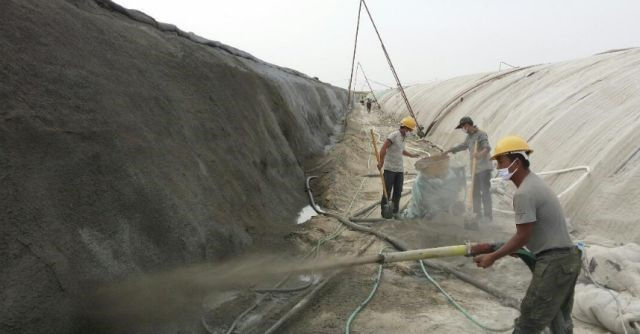
Sprayed concrete has wide-spread use in temporary surface stabilisation and sometimes also used as permanent works. Its field of application includes tunnelling (sprayed concrete tunnel lining), slope stability (usually in combination with ground anchors), mining, surface repair/protection and other funky thin-walled structures. Sprayed concrete sees its presence in all major projects including Crossrail and HS2 which I worked on. In soft ground tunnelling, sprayed concrete is a perfect means of providing temporary face support. Due to the ‘time-space effect’ (see my previous blog https://www.si-eng.org/blog/the-time-space-effect), quick application of temporary face support is required for an excavation, it can be provided effectively by sprayed concrete. Spraying can send concrete onto awkward surfaces with complex geometries, at a distance normally inaccessible by poured concrete.
Sprayed concrete in essence is just another placing method for in-situ concrete, compared to poured (‘normal’) concrete. It delivers almost the same end product compared to normal concrete. It has several ‘side-effects’ due to its particular placing method:
Rebound. When you pour a bucket of water in front of you, or jet-wash your patio, you know your feet are gonna get wet, because of the splash. Sprayed concrete works exactly the same. In particular, the ‘splashing’ of large aggregates is called ‘rebound’.
Wastage. Generally speaking, more rebound = more wastage. How much rebound or wastage depends on several factors including the mix, spraying angle and surface geometry.
Dust. The ‘splashing’ of fine particles will become dust, which can be highly hazardous to health, depending on the additives that go into the concrete.
Compared to normal concrete, sprayed concrete has several distinct requirements related to its particular placing method and field of use:
It must be more workable, i.e. ‘softer’, so that the concrete behaves more like fluid and sprays easier. All concrete contains 4 constituents: aggregate (rock/sand), water, cement and additives (stuff added to concrete that changes its certain behaviours or performance metrics). Compared to normal concrete, sprayed concrete usually contains relatively more water, more sand and smaller aggregate. Plasticizers are also commonly used to avoid excessive use of water.
It should be sticky. Sprayed concrete should shoot out of the nozzle and arrive at its designated surface, stuck firmly to it. Since it takes a lot of pressure to shoot out concrete and the concrete arrives at the sprayed surface at high speed, a lot of cohesion, much higher than normal concrete, is required for it to stick. Lack of adhesion leads to rebound and dust. To increase the stickiness of concrete, additives such as micro-silica can be added into the mix.
It should be able to gain strength quicker. Concrete is a heavy-weight material. Sprayed concrete needs to gain sufficient strength quickly, in order to be able to support its own weight. Otherwise as the sprayed layer thickens, blocks of concrete may fall off the surface when its strength is not enough in supporting its own weight. In some field of applications, such as soft-ground tunnelling, quick strength gain is also desired for deformation control – you want the concrete to become stiff quickly so that it can stop the ground from creeping in. see the ‘time-space effect’ for more information.
Depending on the timing of when cement is mixed with water, sprayed concrete can be categorised into ‘dry-mix’ and ‘wet-mix’.
Dry mix
In ‘dry-mix’, the cement and water get into contact with each other at the last moment before the concrete mix shoots out – they get mixed at the nozzle, and the mixing process is controlled by the nozzleman (the person who controls the spraying nozzle). As such, water is not perfectly mixed with concrete. This means that it produces a large amount of dust and how well they get mixed together is substantially influenced by the skill of the worker, i.e. the nozzleman, which compromises quality control and consistency. There is also ‘pulsing’ effect, which also compromises the consistency of quality.
Wet mix
In ‘wet-mix’, the concrete is fully mixed at the batching plant. What is added at the nozzle is only the accelerator and air pressure. The quality control using wet-mix is much less reliant on the skill of the nozzleman, which can be a scarcity for countries/places where sprayed concrete is not widely used. Because the concrete is sufficiently mixed, everything gels together pretty well, which means there is less dust, and less rebound (concrete get shot onto the surface but does not stick). However, the distance that materials can be pumped is significantly shorter than the dry mix, and it takes a lot of cleaning every time the spraying has to be stopped. Modern and on large scale projects such as Crossrail, sprayed concrete is usually robotised.
Compared to normal concrete, sprayed concrete has the following advantages:
Flexibility. It is able to create complex geometries that would have been impossible with formed concrete. It can get concrete on to bendy, uneven and unstable surfaces. No formwork is required, which means spraying can be done whenever you want, at whatever thickness you need.
Accessibility. Concrete can be sent to the designated surface from a distance far beyond human reach. This can avoid safety hazards such as working at height or working close to unstable excavation surface.
Timely construction. The spraying can be done without any need for formwork or reinforcement, which is extremely valuable for poor ground conditions where time equals deformation (again the ‘Time-Space Effect’ https://www.si-eng.org/blog/the-time-space-effect).
It has the following disadvantages:
Slow construction speed, compared to poured concrete. This may be the primary reason why sprayed concrete is in relatively rare use.
Quality control. Until advanced self-learning robots are put into actual use, sprayed concrete is comparatively a skill-based construction method. The quality of sprayed concrete is substantially influenced by the skill of the nozzleman. Even with robotic spraying, the machine is still controlled by a human. Human controls the spraying speed, thickness, angle, additives. Poor workmanship may lead to:
o Risk of ‘shadowing’. ‘Shadowing’ means the spray can not effectively access the space behind reinforcement, thus creating a void behind reinforcement. To mitigate this risk, small diameter of rebars should be used – say 16mm, with large spacing, say 200mm. As an alternative, fibre reinforcement can be used as a supplement in controlling cracks.
o Lamination. Basically a layer of freshly sprayed concrete is left for too long before another layer gets sprayed on top, creating a ‘cold joint’ in between.
Rough finishing. Because there is no formwork, the surface of sprayed concrete is quite jagged. Sprayed concrete can be used as a permanent structure, but because of its usually undesirable architectural finish, it is more commonly used as temporary works rather than permanent works. In sprayed concrete lined tunnels, sprayed concrete lining can be used as a permanent structure, but usually the finishing is either formed concrete or cladding.
Some tips for designing/using sprayed concrete:
· Sprayed concrete does not have the issue of compaction as normally associated with poured concrete, because of the continuous clashing and squeezing of particles/aggregates under the strong spraying pressure, and the fact that it is more flowy due to higher water content. Like self-compacting concrete (https://www.si-eng.org/blog/self-compacting-concrete) , it does not need vibration.
· Normal concrete has the risk of lack of compaction consequently creating voids, which is called ‘honeycombing’. Sprayed concrete has a similar risk but for a completely different mechanism. Sprayed concrete also has the risk of having voids, but it is caused by spraying onto a surface with obstruction such as reinforcement bars. Usually large or congested reinforcement has a ‘shadowing’ effect, which means a void is created immediately behind the reinforcement bars because the spray can not get to the back of the bars.
· For sprayed concrete in tunnelling, it seems that normal practice for curing normal concrete is seldomly used for sprayed concrete. This maybe because normal cuing practical almost always requires the concrete surface to be readily accessible by workers. Nevertheless, in very dry environment, it is good practice to spray water over the surface to help curing.
· Both ‘over-spraying’ and ‘under-spraying’ (thicker or thinner than intended) need to be avoided, as over-spraying increases risk of block fall and may infringe upon the internal space, whereas under-spraying compromises structural capacity.
· The spraying should be done at a right angle to the surface or at least close to it, otherwise rebound is increased and the density of concrete is reduced

Comments